Dealing with Delays in the Supply Chain: Tips for Jewelers
How to Deal with Delays in the Supply Chain
Introduction: Why the Supply Chain is So Important
As a jeweler, managing your supply chain is crucial for the success of your business. In an industry where precision and timeliness are essential, delays can have huge consequences, from lost customer satisfaction to financial losses. This article offers practical tips for dealing with delays so that you are optimally prepared.
What Are the Causes of Delays in the Supply Chain?
There are several reasons why you might encounter delays in the supply chain. Some of the most common include:
1. Global Disruptions
Factors such as pandemics, natural disasters, or geopolitical tensions can cause significant disruptions. These events disrupt production and transportation, leading to delays.
2. Insufficient Inventory Management
A lack of efficient inventory management can also cause delays. If you don't have enough stock, you may have to wait for new deliveries, which can result in missed sales opportunities.
3. Limited Transportation Capacity
The shipping industry can be overloaded, especially during peak seasons. This can lead to longer delivery times that you can't always foresee.
Pro tip: Conduct a SWOT analysis to better understand the risks and opportunities in your supply chain . This will help you anticipate potential delays.
How to Prepare for Delays
Prevention starts with good preparation. Here are some ways to prepare for possible delays :
1. Diversify Your Suppliers
If you rely on a single supplier, you are vulnerable. Diversify your suppliers to spread risks, so you always have an alternative option if something goes wrong.
2. Invest in Technology
Using an advanced cash register system can help you optimize your inventory management and anticipate delays. Technology allows you to collect real-time data, enabling you to respond to changes more quickly.
3. Maintain Good Relationships with Suppliers
A good relationship with your suppliers can make a difference. By keeping open communication and regular follow-ups, you can identify problems earlier and find solutions together.
Pro tip: Regularly schedule meetings with your suppliers to get updates on their delivery capacity and any challenges they are facing.
How to Deal with Delays When They Occur
Even with the best preparations, delays can still occur. Here are some strategies for dealing with this situation:
1. Communicate with Your Customers
If there's a delay, it's important to inform your customers as soon as possible. Transparent communication builds trust and can help customers show understanding.
2. Offer Alternatives
Instead of just waiting for delayed deliveries, you can offer customers alternative products or solutions. This keeps your customers satisfied and may encourage them to buy from you again in the future.
3. Review Your Plans and Strategies
Use this experience as a learning opportunity. Analyze what went wrong and adjust your strategies to prevent future issues.
Pro tip: Use customer feedback to improve your current processes. Customers can provide valuable information on what they find important during a delay.
Effective Technologies for Managing Delays
Technology can help you manage delays effectively. Here are some tools and systems you might consider:
1. Inventory Management Software
Good inventory management software is essential for keeping track of your products. It ensures that you are always aware of your inventory management and can respond quickly to changes.
2. Project Management Tools
Tools like Asana or Trello can help you track projects and manage deadlines. This is especially important when working with multiple suppliers and stakeholders.
3. Customer Relationship Management (CRM)
A CRM system can help you track customer communications, as well as their preferences and needs. This can be vital when adjusting your offerings during delays.
Pro tip: Never just evaluate the technology you have; also consider the training and support your team receives. This can significantly impact the success of using new technologies.
How to Optimize Your Supply Chain for the Future
After dealing with delays , you want to ensure your system is future-proof. Here are a few strategies:
1. Evaluate Your Current Processes
Regularly conduct audits of your supply chain to determine where improvements can be made. This can help you gain more control over your supply chain .
2. Invest in Training for Your Staff
A well-trained team is better equipped to manage supply chain issues effectively. Ensure your employees are well-informed about the latest technologies and processes.
3. Stay Updated on Industry Trends
The world of jewelry is constantly changing. By keeping up with trends and developments in the industry, you can timely adjust your strategies.
Pro tip: Join industry organizations. This can provide you with valuable networking opportunities and access to information that can help improve your business.
Conclusion
Dealing with delays in the supply chain can be challenging, but with the right strategies and tools, you can overcome these obstacles. By being well-prepared, effectively communicating with customers, and utilizing technology, you can keep your jewelry business running smoothly.
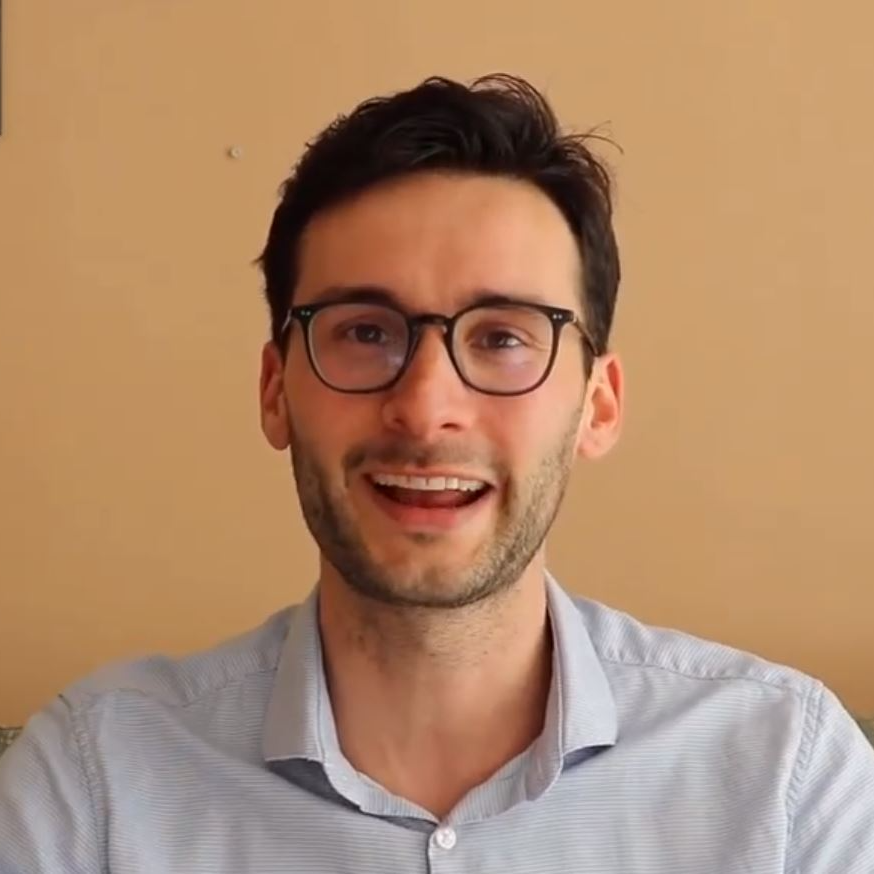
Take your store to the next level
Start automating and digitizing your store processes today. PrismaNote helps retailers with this. Discover what we can do for you via the menu above.
- George
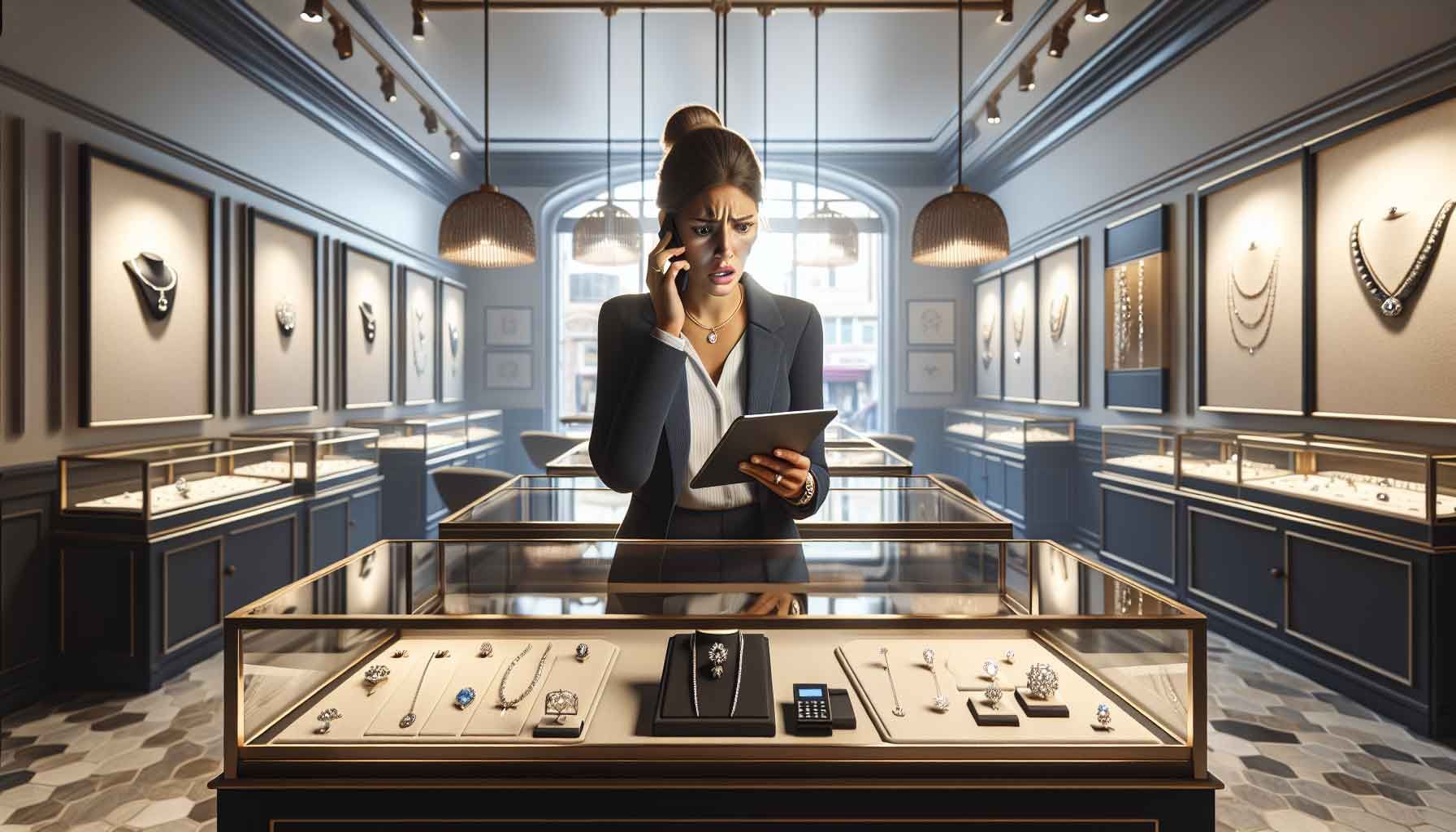