Specifications of the Work Order that are Crucial
Work orders are crucial in any repair project. They serve as the backbone of the process, from recording customer information to documenting the work performed. A perfect work order ensures clarity, prevents misunderstandings, and helps manage the project efficiently. In this blog post, we discuss the specifications that make a work order an indispensable tool.
The Essential Specifications of the Work Order for Repair Projects
1. Customer Information
The foundation of every work order starts with clear and complete customer information. This includes:
- Customer Name: Include the full name to avoid confusion.
- Customer Address: In a location, multiple people can have the same surname. Therefore, always note the address as well.
- Contact Information: Phone number, WhatsApp, and email address for quick communication.
- Customer Number (if applicable): For businesses with repeat customers, a customer number can simplify management.
2. Project Details
This section lists the core details of the repair project:
- Project Name: A brief description or title of the project.
- Unique Reference Number: Each project must have a unique number for easy identification and reference.
- Barcode: This saves a lot of time when processing the repair.
- Start and End Date: When the work begins and when it should be completed.
3. Work Performed
This should be as detailed as possible:
- Description of Work: A detailed list of the tasks that were performed.
- Materials and Parts Used: Specify the materials, parts, and their quantities. Including serial numbers can be useful, especially for warranties.
- Hours Worked: The number of hours spent on each task, possibly broken down by employee.
4. Costs and Price Specification
Transparency in costs is essential:
- Cost per Item: The price of each part or material used.
- Labor Costs: Hourly rate and total number of hours, clearly broken down.
- Additional Costs: Any extra costs, such as travel expenses, should be clearly mentioned.
- Subtotal and Total: Clear layout of subtotal costs and the total amount including VAT.
5. Approval and Signature
Is it about expensive repairs? Then it might be interesting to ensure legal clarity. In this case, the work order should allow for approval:
- Customer Signature: Confirmation that the customer agrees with the work done and the costs.
- Executor Signature: Confirmation that the work has been completed according to the agreed specifications.
- Date of Signature: For both the customer and the executor.
6. Warranties and Conditions
Including warranty information can help prevent future disputes:
- Warranty Period: Clearly mention the warranty period on the work performed and the parts used.
- Terms and Conditions: Any important conditions or exclusions that apply to the warranty.
7. Follow-up Appointments
For projects that may require multiple visits:
- Date of Next Appointment: If applicable, when the next work is scheduled.
- Requirements for the Next Phase: List of materials or preparations needed for the continuation.
8. Space for Comments
An open section for notes can be useful:
- Customer Comments: For feedback or special requests from the customer.
- Internal / Technical Comments: For the technician to note any particulars that may be important for future reference.
A perfect work order is more than just a simple document; it is an essential tool for organizing and managing repair projects. By ensuring completeness, clarity, and transparency, a well-designed work order not only aids in executing the current project but also builds trust with the customer for future projects.
Make sure your work order meets these specifications, and you will find that managing repair projects goes much more smoothly.
How Repair Software Can Help in Creating Work Orders
In the jewelry industry, precision is crucial. Every mistake can result in avoidable losses, fragmented time, and frustrated customers.
Work orders and invoicing software automate and streamline processes that would otherwise be time-consuming and error-prone.
Imagine: you no longer need to fill out paper work orders or manually chase invoices. Therefore, use good repair software with a user-friendly interface and features specifically designed for the jewelry industry, such as inventory management and customer history.
Key Features of Work Order Software
When you are looking for the best work order and invoicing software, there are several crucial features to look for.
- Automation: Automating work orders and invoicing is key to efficiency. Automatic reminders and workflows save you time and reduce errors.
- Integration with Existing Systems: Your new software should integrate seamlessly with your current systems, like inventory management and CRM software. This prevents data silos and ensures a streamlined process.
- User-Friendliness: Not everyone is a tech expert. Choose software that is intuitive and easy to use for you and your staff.
Pro Tip: Look for software with mobile or tablet capabilities. This helps staff in the workshop or on the go easily access all the necessary information.
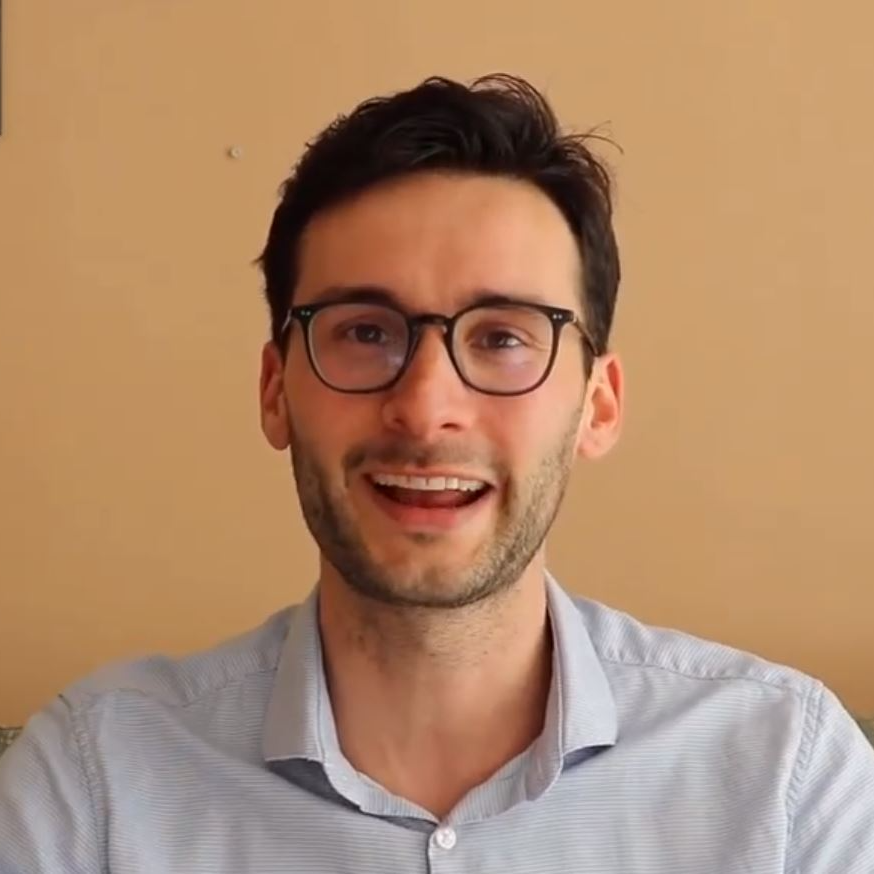
Take your store to the next level
Start automating and digitizing your store processes today. PrismaNote helps retailers with this. Discover what we can do for you via the menu above.
- George
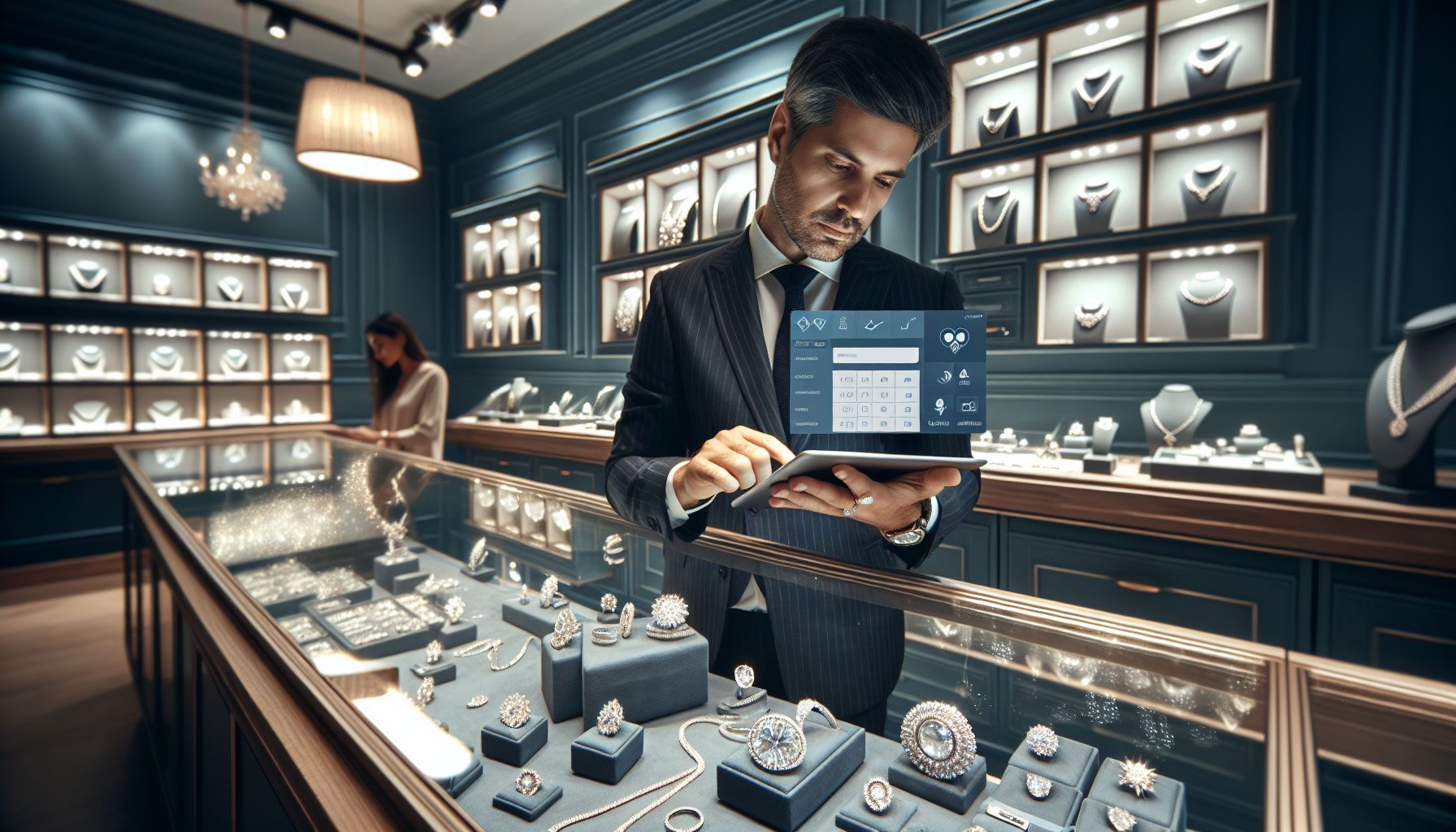